According to Deloitte, it’s estimated that poor maintenance strategies can reduce a plant’s overall production capacity from between five to 20%.
Industry is becoming more sophisticated in its approach to predictive maintenance, particularly through the use of smart sensors. An important first step in developing a predictive maintenance strategy to identify asset or component criticality — and it turns out that one way to do this is with a small component that has been widely relied upon in machines and equipment for decades.
Modern manufacturing relies heavily on bearings. They are used widely in almost every type of rotating equipment, and the global bearings market is expected to reach $186.1 billion by 2025, according to Grand View Research. At the same time, demand is also growing for bearings with lower maintenance requirements, longer lifespans and more efficient performance capabilities. This is driving developments in smart bearings.
Chris Johnson, managing director at SMB Bearings, explains that smart bearings with builtin sensors have been widely used in automotive anti-lock braking systems (ABS), for years, and are now being increasingly adopted by industry. At the same time, more manufacturers are making use of Industrial Internet of Things (IIoT) technologies to remotely monitor their processes and translate physical actions from machines into digital signals.
Against this evolving Industry 4.0 backdrop, he adds that bearings and their performance remain essential to the effective performance of plant machinery: “After all, it is more favourable to replace a single bearing in an electric motor than to replace the entire motor. And it’s even better to choose the right bearings in the first instance, which is where manufacturers can opt for smart bearings.”
But, what are the benefits of smart bearings? Johnson explains that they offer the logical next step in maintenance, especially predictive maintenance: “IIoT-based smart bearings can self-diagnose impending faults and failures, based on data from sensors integrated into the housing of the bearing itself.”
One example he highlights is wheel hub bearings with built-in sensors manufactured by SKF that are used to detect the speed, position and direction of rotation in ABS brakes. Another is the EZlink monitoring system developed by Rockwell Automation and Dodge. Sensors are used to glean data from up to 62 bearings — on the bearings’ temperature, vibration, or speed — which is then communicated to an industrial control system.
These are just a couple of examples of how built-in sensors can aid performance in industrial equipment and play a vital role in continued IIoT integration.
Through dealings with its own customers, Johnson, says his company has seen first-hand the potential of smart bearings to predictively monitor machine processes, in real-time, during machine operations. Speed, pressure, force, temperature and vibration can all be monitored — and each can provide critical data.
However, he comments that it’s important to note that data from smart bearings should be analysed alongside data collected from other critical assets, to provide a holistic view of operations: “Used properly, smart bearings offer the possibility of an extended bearing service life, lower energy consumption and the prediction of early equipment failure.”
Component manufacturers are also getting on board with smart bearings, while bearing manufacturers are developing relationships with innovative IIoT companies, to provide businesses with extended cloud predictive maintenance services for a range of industrial machines. There is also the possibility to reduce training costs associated with predictive maintenance, as less-experienced operators can reach desired performance levels more quickly.
While it’s not possible to foresee the onset of a tooth cavity, smart bearings with predictive maintenance capabilities hold many advantages for industry — and their use is expected to significantly increase in aerospace and defence, wind turbines, railway and automotive segments. By using affordable sensors, manufacturers can ensure that critical machine components play a crucial role in preventing equipment failure, and that bearings are more crucial to this than ever before.
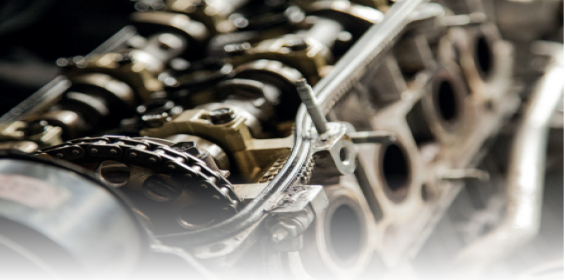