When specifying control valves, ensuring the right input data is provided offers the best chance the resulting performance of the application will be optimised. To show the effects, a recent example based on deionised water production highlights how accurate specification is essential whenever control valves are used. Full consideration of the application’s key criteria, as well as accurate calculation of input application data, are vital to optimise control valve specification.
Recently, a system integrator approached Bürkert to supply a valve for a water conductivity blending application, with the objective of achieving water quality with a conductivity level of 10μS (microsiemens). Their process design schematic included a ball valve that would isolate the flow of softened water, while a control valve would modulate the flow of deionized water. By controlling this media combination, once blended, the customer’s expected outcome was water production at the desired conductivity level. With this plan, the system integrator requested a control valve that would regulate the deionized water flow.
To calculate the size of control valve required, it is important to understand the required flow rate and pressure. The integrator suggested that upstream pressure was 4 bar, with 3 bar pressure downstream. Moreover, they suggested a total flow rate of 1.5 m3//h. Even at this stage, Bürkert suggested a review of this input data because the suggested flow rate appeared to be inaccurate. Furthermore, using the pressure and flow data, the calculation generated a requirement for a 1” diameter valve, which would likely be too large for this application. However, the integrator was satisfied with the validity of their initial input data, and they confirmed the resulting valve specification, supported by the fact that they had used this size of valve on a similar project with the same input data.
Oversized valve specification
The Bürkert team remained unconvinced and they sought wider input data to help confirm the specification. The integrator reported that when installed, the previous valve project would operate at 10 to 20% of its total capacity. However, the reverse situation should ideally apply, sizing a valve to operate at 70%-90% of its capacity would enable the use of a smaller, more cost-effective valve, that could also achieve more efficient operation.
Burkert decided to recalculate the valve size, based on optimising 80% capacity. This time, to ensure a comprehensive approach, the input data was reconfirmed. With a reading from the system’s pump, the upstream pressure was confirmed. Thanks to an installed flow meter, the flow reading was also verified. Using these input data, it was possible to work backwards and determine the actual downstream pressure.
This highlighted that the downstream pressure was significantly less than the figure initially provided. Instead of the suggested 3 bar, the new calculation was just 0.1 bar. Based on this new data, it was realised that the customer’s desired, repeatable, and controllable flow range could not be achieved
Optimising control accuracy
On further investigation, the customer revealed that an open tank was positioned downstream of this system, which both explained and confirmed the almost 0 bar downstream pressure reading. As a result, the customer agreed to resize the valve, sufficient to handle a difference from 4 bar upstream pressure down to 0 bar downstream.
By this stage, the system integrator was working more closely with Burkert, and as a result, were also able to challenge a fundamental assumption about the system’s design. Although the conductivity value of the deionized water was very low, at 0.5 μS, the value of the softened water was very high, around 600 μS.
Without modulating the softened water flow, the resulting conductivity level after blending the media would be far higher than the objective of 10 μS. Bürkert advised that instead of regulating the flow of deionised water, by controlling the softened water, the desired conductivity level could be reached.
Get it right first time
Switching the position of the control valve and resizing it accordingly enabled the integrator’s system to achieve the low, 10 μS water conductivity rating for their customer. Without assistance in making the correct calculation, the customer would have integrated a much larger – and much more expensive – control valve. Most significantly, the system would have been far less likely to have produced the desired quality of water. Had the system designer engaged with valve sizing and application expertise at the outset, they would also have avoided rework in design, instead achieving a faster time to market.
Although this example demonstrates specific implications of incorrect specification, the same principles apply for any application that requires control valve modulation. The fundamental calculations to ensure correct control valve sizing are essential whatever the purpose and sector, from food & beverage, to pharmaceutical and life sciences.
A crucial aspect for optimum sizing of control valves is achieving valid application input data. If the input application data is incorrect, or incomplete, then the type, position, and size of the control valve will be sub-optimal. While specifiers can make mistakes in calculations, valve specification errors can also have historic origins. If the original system wasn’t designed according to the right data, like-for-like replacement will also be sub-optimal. As technology has advanced, valves today are frequently more accurate, impacting open and close rates, and this means that smaller, less expensive valves can potentially be used instead. So, even when upgrading an existing system, the best practice is to recalculate control valve sizing each time
********************************************************************************************************
Valve sizing
Bürkert’s process valve sizing tool, comprising control valve selection, helps designers and specifiers configure the right specification through a sequential set of application criteria. This tool helps to make control valve selection fast and simple, however, it’s imperative to remember that valve specification depends on valid input data.
Moreover, when used in an application like conductivity blending, Bürkert has additional internal tools to determine whether a complete system could achieve the desired outcome.
The surest way to achieve optimised valve specification, first time, is to involve a flow control specialist as early as possible in the process. Sharing access to details on the wider application enables an experienced valve provider to make an accurate specification based on all of the relevant criteria. This process might involve challenging the input data, but in so doing, a more effective outcome can be achieved.
********************************************************************************************************
https://twitter.com/BrkertUKIreland
https://www.linkedin.com/company/burkertfluidcontrolsystemsuk&ireland/
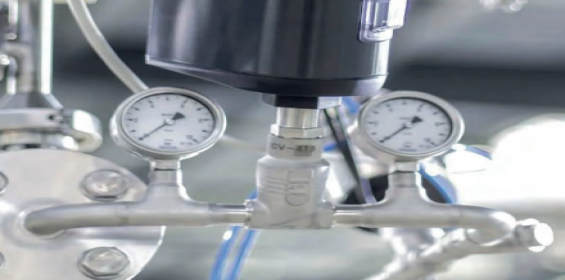