Aside from the negative impact of CO2 production on the environment, there is also
the financial burden of energy usage. For this reason, manufacturing companies are actively exploring ways to lower their carbon footprint and enhance energy efficiency.
One area that offers manufacturers a significant opportunity to reduce CO2 emissions is by recovering the waste heat from air compressors. While this approach has gained some traction in Europe, the adoption of compressed air energy recovery has been slower in the UK. The perceived complexity of heat recovery systems has contributed to the slow uptake. Nevertheless, research shows that significant benefits can be gained. The experience of those already pursuing this strategy confirms this data.
Statistics show that compressed air typically accounts for about 12% of the total energy costs for industrial manufacturers. For some facilities, the figure may reach as high as 40%. However, 70-94% of energy consumed by air compressors is recoverable. Without any form of recovery, this energy is lost through radiation to the atmosphere or through cooling systems. The carbon equivalent of every kW of energy saved makes this a viable target for CO2 reduction measures.
How compressing air generates heat
Compressing air generates heat. This is a natural consequence of forcing more air molecules into the same space. The problem is that the air must be cooled before it can be used. In many systems, the air is cooled between compression stages and then again at the end. Intercoolers remove heat between the first and second stage and after-coolers remove heat after the second stage.
How heat can be recovered in compressed air systems
Coolers remove heat from compressed air using air, water or oil. They work on a system of heat exchange. The air transfers heat to the cooling medium in a cooler designed for the compressor flow rate and energy transfer requirements. There are different types of cooling systems used in air compressors. Each one has advantages and disadvantages, and some can recover up to 94% of the supply energy to the air compressor.
Levels of heat recovery
Air-cooled systems are common in small and medium compressor systems. They cool compressed air using a lower pressure air stream. This warmed air can then be used to heat buildings. The energy-saving comes from a reduction in heating purchased from external sources. Unfortunately, this saving can only be realized in the colder months of the year.
Oil-cooled systems use a flow of oil to remove heat from the compressed air. In a closed system, the oil can be routed back into the manufacturing process. Heat is transferred into the manufacturing process in a heat exchanger, thus reducing the need for electric or gas heating.
Water-cooled systems can be open or closed and circulating or non-circulating. The most useful is a closed-loop system with circulating water. Water circulates between the air compressor cooler and a process heat exchanger. The net result is a transfer of excess compressor heat into the manufacturing process, thus reducing the need for heating. In a closed-loop system water quality is strictly controlled using additives, which prevents the build-up of mineral deposits. As such, the system is efficient and clean and can remain operational for a long period without intervention.
In every case, recovering heat from compressed air reduces the need for purchasing energy. It is this reduction that results in lower CO2 emissions and operating costs. Due to the high cost of energy, these savings can be significant in terms of helping companies to meet their carbon reduction targets and improve manufacturing plant profitability
Case studies of compressed air heat recovery
By using an oil coolant in their ER-S5 energy recovery unit, a Midlands-based automotive textiles manufacture was able to recover heat from its air compressor outlet. Hot oil from the air cooler transferred energy into the process via a steel plate heat exchanger. This gave them a continuous supply of hot process water without any extra energy purchase. As a result, the company was able to reduce CO2 emissions by 260,000 tonnes per year by using this recovery method.
A packaging plant in Northern Ireland found a different use for recovered energy. Greiner Packaging uses its excess heat to contribute to the central heating system of a local secondary school. Dungannon Integrated College has 600 pupils and uses £40,000 of heating on an annual basis. In this case, Atlas Copco installed Z-range oil-free screw compressors with water coolers for energy recovery. Up to 80% of the electrical input energy is recovered as hot water. The school also reduced its CO2 footprint by 200 metric tons through reduced energy purchase.
The untapped potential of heat recovery
These case studies demonstrate both the environmental and financial opportunities of investing in compressed air heat recovery, yet most industrial companies in the UK are still yet to embrace and realise the benefits of the technology. Indeed, it is estimated that 90% of all industrial air compressors used in the UK could be equipped with heat recovery systems. And, as stated above, 70-94 % of the supply energy to an air compressor can be recovered.
To illustrate the vast untapped potential of compressed air heat recovery, it is calculated that the technology could save 1.99% of the total industrial electricity consumption in the UK. If that statistic isn’t compelling enough, it is the equivalent of removing the emissions from 913,000 diesel/petrol cars per year, or recovering the energy required to power 1.544 million households’ electricity consumption per year. Now, if that isn’t a compelling case for compressed air heat recovery, it’s difficult to say what is.
*Calculations are based on total industrial electricity consumption in the UK, and an average of 10% of industrial electricity consumption being used by compressors.
*Approximately 70% of energy is recoverable from oil-injected screw compressors, and up to 94% from oil-free water-cooled screw compressors.
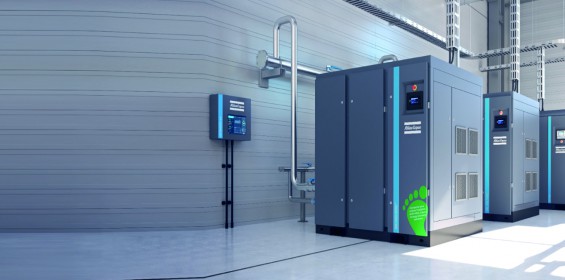